In the fast-paced world of manufacturing, efficiency, protection, and sustainability is paramount. One often overlooked but crucial element that plays a pivotal role in achieving these goals is engineered foam packaging. These seemingly simple materials provide a multitude of benefits that contribute to the success of manufacturing processes across various industries. In this article, we will explore the importance of engineered foam packaging within manufacturing, shedding light on its role in safeguarding products, enhancing operational efficiency, and the benefits in the wood packaging industry.
Protecting Precious Cargo
Manufacturers deal with an array of delicate and valuable products daily. Whether it’s electronics, automotive parts, military equipment, or pharmaceutical products, ensuring these items arrive at their destination intact is imperative. Engineered foam packaging excels in this regard, as it offers unparalleled protection against shocks, vibrations, and impacts during transit.
One of the primary advantages of engineered foam packaging is its ability to conform to the shape of the product, providing a snug and secure fit. This customized protection minimizes movement and prevents items from hitting each other or transportation walls, significantly reducing the risk of in-transit damage. This is especially crucial for manufacturers shipping globally, as products endure long journeys and potentially rough handling.
Understanding Engineered Foam Packaging
Engineered foam packaging, at its core, refers to the use of various foam materials, such as expanded polystyrene (EPS), polyurethane foam, or polyethylene foam, to cushion, protect, and secure products during transit. This versatile packaging solution comes in various forms, including foam sheets, custom-molded inserts, and foam rolls, all designed to meet specific requirements.
Types of Engineered Foam Materials
Lightweight and versatile, EPS foam is known for its excellent shock-absorption properties. It is often used to create protective inserts for wood products.
This flexible and durable foam is used for cushioning and padding. It can be tailored to fit different product shapes.
Polyethylene foam is resistant to moisture and chemicals, making it suitable for protecting wood products in harsh environments.
Enhancing Operational Efficiency
Efficiency is the backbone of any successful manufacturing operation. Engineered foam packaging plays a pivotal role in streamlining various processes and reducing downtime. Here’s how:
Time Savings:
Engineered foam packaging materials are readily available in various forms, such as foam sheets, inserts, and custom-molded shapes. This accessibility allows manufacturers to quickly adapt their packaging solutions to meet specific product requirements, saving valuable time in the production line.
Easy Handling:
Engineered foam packaging is lightweight and easy to handle, making it efficient for assembly line workers to integrate into their processes. Unlike bulkier and heavier alternatives, engineered foam packaging doesn’t add unnecessary labor costs or slow down production.
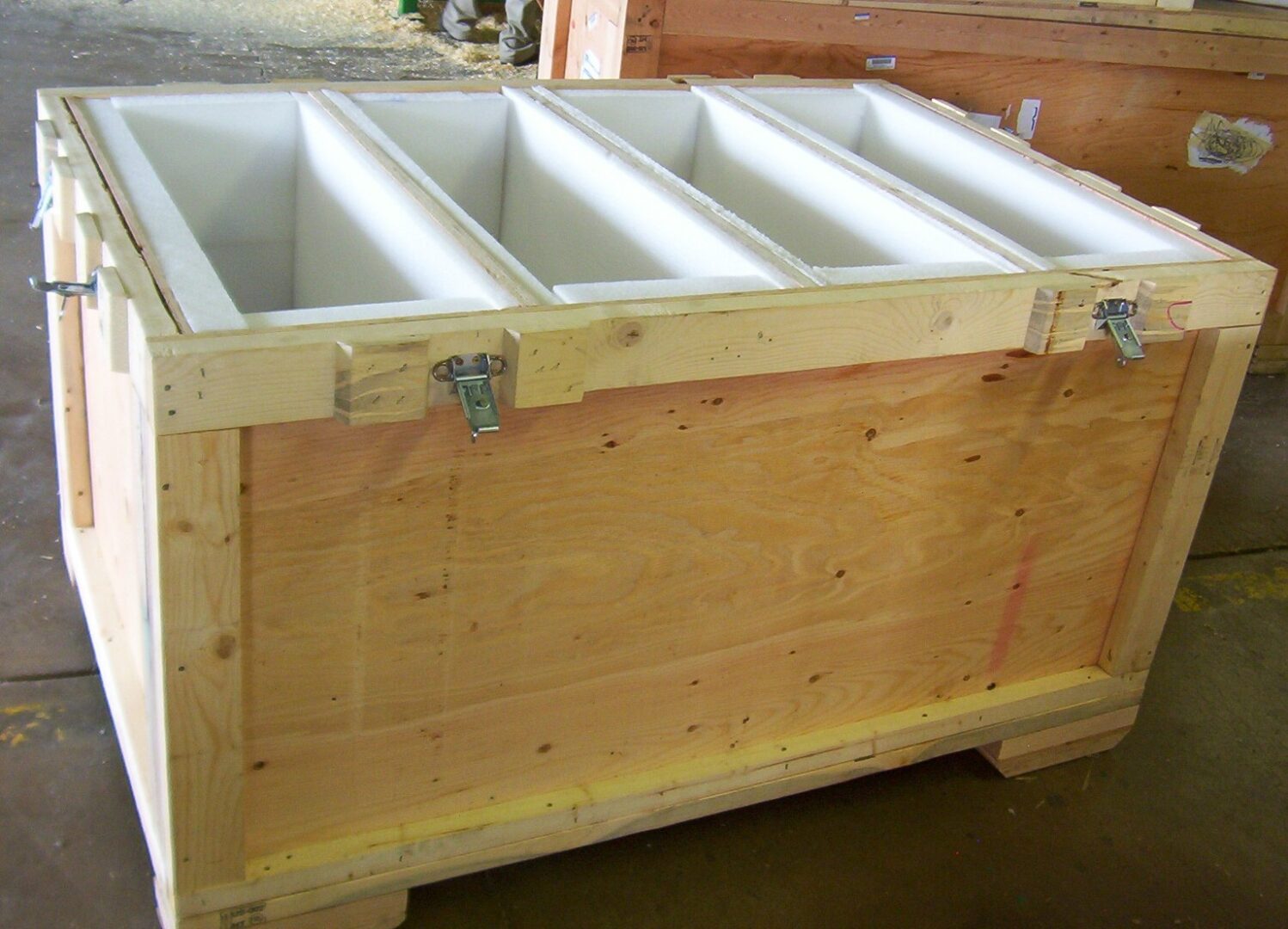
Customization:
Engineered foam can be customized to fit any product, regardless of shape or size. Manufacturers can create tailored solutions that maximize space utilization within containers, leading to more efficient shipping and reduced packaging waste.
Inventory Management:
The versatility of engineered foam packaging allows for better inventory management. Manufacturers can stock a range of foam materials and easily adjust their usage based on changing product lines or shipping needs.
Benefits of Foam Packaging in the Wood Packaging Industry
Now that we’ve defined engineered foam packaging, let’s explore why it is a game-changer in the wood packaging industry.
Protection of Products:
Engineered foam adds another layer of protection to your products that are being shipped with wood packaging. Engineered foam can be cut to fit exact measurements, which will keep products snug without damaging them.
Shock Absorption:
During the transit process products can experience sudden drops, strikes, or the jostling vibration of a truck. Engineered foam’s inherent ability to absorb shocks and vibrations provides a soft cushion that safeguards wood products against impacts during handling, shipping, and storage.
Preventing Scratches and Scuffs:
Engineered foam packaging forms a protective barrier that prevents surfaces from coming into direct contact with each other or with other materials, reducing the risk of scratches, scuffs, and abrasions. Engineered foam can make sure that your products are not being damaged, even slightly, before making it to their destination.
Moisture Protection:
Some foam materials, like polyethylene foam, are moisture-resistant, ensuring that wood products remain dry and unaffected by humidity or inclement weather conditions.
Reduced Labor Costs:
Lightweight foam packaging is easy to handle, minimizing the physical strain on workers during the packaging process and reducing labor costs.
Improved Stacking and Palletization:
Foam packaging can be designed to create stable stacks of wooden products, minimizing the risk of damage from uneven stacking, or shifting during transport.
Sustainability Matters
As customers become increasingly conscious of environmental issues, sustainable manufacturing practices are more critical than ever. Engineered foam packaging is not exempt from these concerns, but advancements in materials and recycling processes have made it a viable option for environmentally responsible manufacturing. Here’s how engineered foam packaging contributes to sustainability:
Recyclable Options:
Many engineered foam packaging materials are now recyclable, reducing the environmental impact. Manufacturers can choose from recyclable foam materials like expanded polystyrene.
Waste Reduction:
Customized engineered foam packaging minimizes waste by using the exact amount of material required to protect each product. This reduces the overall volume of packaging materials and promotes a more sustainable supply chain.
Energy Efficiency:
Engineered foam manufacturing processes have become more energy-efficient over time, reducing the carbon footprint associated with their production. Additionally, lightweight foam packaging reduces transportation energy costs.
Reusable Options:
Some engineered foam packaging solutions can be designed for multiple uses, further extending their lifespan, and reducing the need for frequent replacements.
The Future of Engineered Foam Packaging in Manufacturing
The importance of engineered foam packaging within manufacturing is poised to grow even further as innovation continues to drive the industry. Here are some emerging trends and developments:
Smart Packaging:
Incorporating sensors and RFID (Radio-Frequency Identification) technology into engineered foam packaging can provide real-time tracking and monitoring of products during transit, enhancing supply chain visibility.
Material Advancements:
Ongoing research into eco-friendly engineered foam materials and advanced manufacturing processes will yield even more sustainable options, reducing the environmental impact of foam packaging. Conner is dedicated to innovation and keeping up with industry trends to provide our customers with the best possible product.
Customization with 3D Printing:
3D printing technology is making it easier to create highly customized engineered foam packaging solutions, optimizing protection and efficiency.
Circular Economy Integration:
Manufacturers are exploring ways to integrate engineered foam packaging into circular economy models, promoting reuse, recycling, and repurposing of materials.
Wrap It Up
In conclusion, foam packaging is a silent hero in the world of manufacturing, offering critical benefits that protect products, enhance operational efficiency, and support sustainability efforts. As manufacturing continues to evolve, so will the role of engineered foam packaging, proving that these unassuming materials are an indispensable part of the modern production landscape. Manufacturers who recognize and harness the potential of foam packaging will gain a competitive edge in an increasingly dynamic and demanding market.
Conner is dedicated to our integrated packaging division and supplying customers with the perfect transportation packaging. With our newest acquisitions specializing in integrated and engineered foam packaging, we are poised to serve customers in the rapidly evolving environment. Work with a supplier that can take care of all your needs today!