Don’t overlook the benefits and cost savings of foam packaging!
Wooden packaging products, such as pallets, crates, and integrated packaging, are critical items in the transportation of products, commodities, and raw materials around the world. They not only provide a secure means of transport for goods but also ensure that the products remain intact and undamaged during transit. However, products can be prone to damage during the transportation process if proper precautions are not taken. That is where industrial foam packaging comes in, to protect products.
Foam packaging was invented during World War II, with its original use being a floatation device for the military. Shortly after, it became clear that foam packaging would be a great safety net within transportation, as it provides cushioning, while taking up less space and weight in-transit. Let’s dive into what foam packaging is, what the uses are, and how you can benefit.
What is Foam Packaging?
Industrial foam packaging is a popular and practical solution in the wood packaging industry. Industrial foam packaging is made from various materials, including polyethylene, polyurethane, and expanded polystyrene (EPS). This kind of foam packaging is used to provide protection for the products that are being transported.
Polyurethane Foam:
Polyurethane foam (PU) is lightweight and has a soft surface. This allows it to be easily shaped to fit different packaging and products. Typically, it is used for items that need scratch resistance, such as glass and electronics. It is very effective at protecting sensitive items and can lessen any vibration damage.
Polyethylene Foam:
Polyethylene foam (PE) is denser and harder than PU foam packaging, which makes it ideal shipping products that require more stability, like heavy machinery or breakable items. It has high shock and vibration qualities that make it more durable than other foam packaging. PE is available in different densities and thicknesses, depending on what is needed for the product being transported.
Expanded Polystyrene Foam:
Expanded Polystyrene foam, otherwise known as Styrofoam, is the cheapest and most versatile of all the foam packaging options. It is a durable, insulated, lightweight, and efficient material that can help to prevent in-transit damage to products. It must be used in conjunction with other packaging if protecting against shock is a priority.
Why Use Foam Packaging?
Industrial foam packaging is an important innovation in the manufacturing industry because it adds a new layer of protection for the goods being transported and helps to eliminate the risk of damage together with the wood packaging used. The foam is custom designed to fit a specific item or space. This ensures that the foam packaging provides maximum protection and maintains the integrity of the entire shipping unit. The foam packaging is soft and flexible, which makes it effective in absorbing shock. Industrial foam packaging is structured to protect the items against moisture and mildew too.
Foam packaging is custom designed to fit a specific item or space. This ensures that the foam packaging provides maximum protection and maintains the integrity of the entire shipping unit. Click To TweetThree types of common in-transit damage that can occur during transportation are:
1. Impact:
While in-transit or when being shipping/ received products can experience sudden drops or have something else strike them. It is not uncommon for a pallet to be loaded indirectly causing a fall with products inside. Foam packaging helps to stabilize the product within crates and pallets to ensure that there is another barrier of safety.
2. Vibration:
Vibration damage is common because products will likely be subjected to the jostling from the motors of trucks, trains, and planes. Common issues that vibration can cause are structural integrity loss, loosening of fasteners, and loss of aesthetics. Foam packaging can provide support in keeping products in place within wood packaging, which prevents vibration damage.
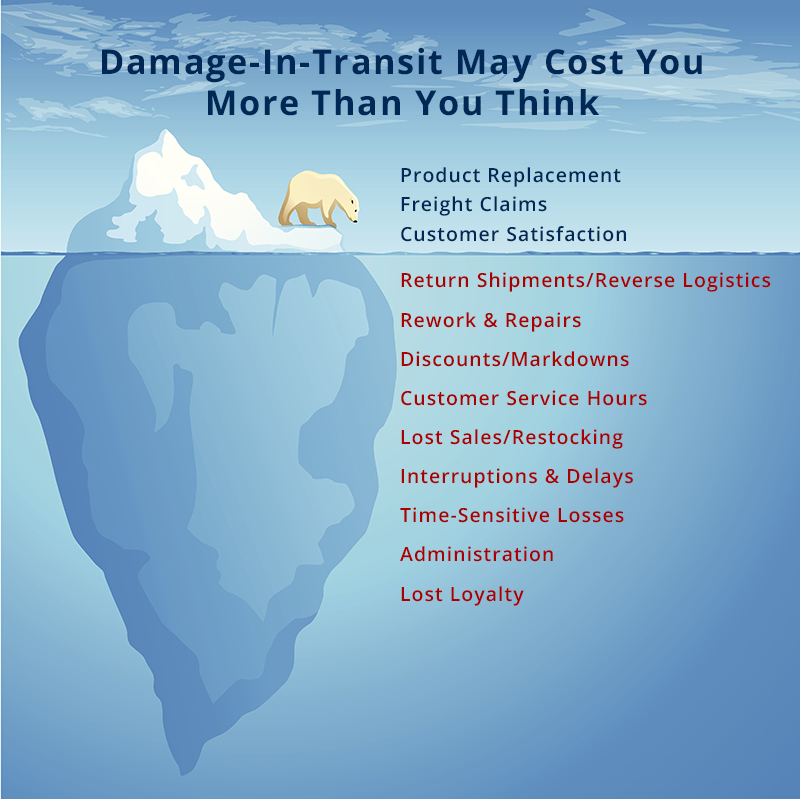
3. Compression:
Compression damage can happen with improper packaging of products. This can happen within the wood packaging itself or when it is loaded to be transported. Using the wrong straps, banding groove, or securing too tightly can cause compression damage to occur. Foam packaging once again gives a barrier of protection to help prevent damage.
Benefits That Pay Off
Another added benefit of using industrial foam packaging is that it’s lightweight, which results in lower transportation costs. This is because the less weight a shipment has, the less it costs to ship it, and it also helps to minimize fuel consumption. In addition, it can prevent the extra costs that come with in-transit damage. In-transit damage can add up very quickly and prevention is key.
Wrapping It Up
In conclusion, industrial foam packaging has proved to be a useful tool in the wood packaging industry. It’s an efficient way to protect products during transport as well as being weight and cost friendly.
Work with a supplier that can help design your integrated packaging, that includes foam packaging, to guarantee your products’ safety. Selecting a supplier with knowledge and expertise in the integrated packaging field will improve your packaging and your supply chain as a whole. Don’t wait, reach out to learn more about foam packaging today!