While there are several key factors required to make a well-designed wood pallet or crate, arguably the most important is using the proper fasteners for the job. From crates to pallets to stand alone shelving, the right choice in fastener will make all the difference in that product’s longevity, durability and strength. Knowing what type of fastener is best for your application, how large they need to be to perform as needed, and how many fasteners are required can be the difference between getting your cargo to its destination safely or watching your wood packaging fail under the stress of use.
Most Common Types of Fasteners
Although there are many different types of fasteners and variations on fasteners available in the marketplace for a wide variety of uses and industries, the most commonly used fasteners in the wood packaging industry are nails, screws, and staples. The type of fastener used for a particular application can depend on a lot of different factors, but the most effective selection provides the most appropriate combination of strength, longevity, and cost-effectiveness.
Without consideration given to each of these factors, the wrong fastener may be chosen and result in a pallet or crate failure, whether immediate or after long-term use.
Fastener Type 1: Nails
The classic nail has been around for generations and has seen a few different methods of creation to reach the nail form that we see today. Before nails found their way to mass production, they were hand-made by artisans called “Nailers” out of wrought-iron. Mass producers later began cutting nails from large sheets of iron, allowing iron fibers to run the length of the nail to give it the added strength that was lacking in handmade versions.
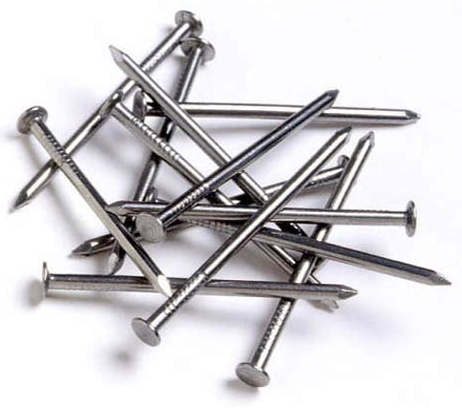
By 1913, this method was replaced, and over 90% of nails were made from steel wire. The new steel wire nails offered a variety of diameters cast from different gauge wire, and could be adjusted according to the die and the specific diameter needed. Modern nail production continues in this tradition.
Today, nails are the most widely used fastener in the wood packaging industry, and are usually applied using a pneumatic nail gun – although a hammer works too.
Fastener Type 2: Screws
Just like nails, screws were also once made by hand, and have proven to be a superior choice for joining materials. Screws also have the added advantage of being easily removed from most products without damaging the material itself, which is often why they are chosen over nails.
You simply unscrew it.
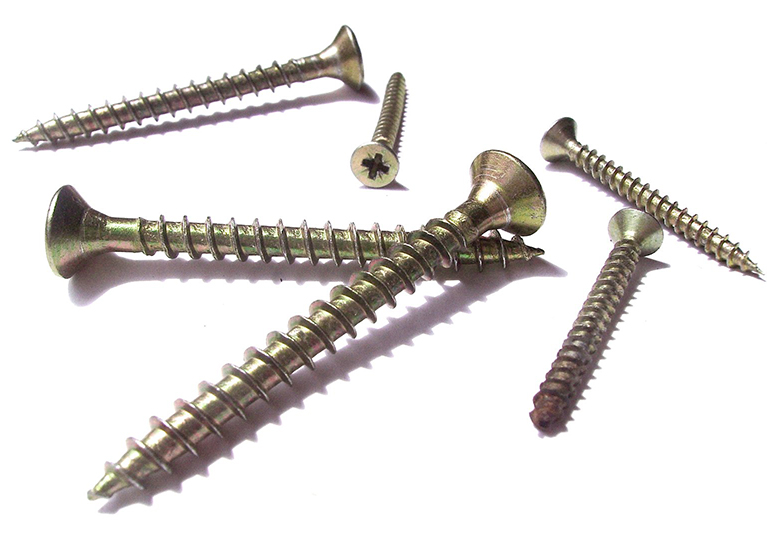
These types of fasteners are applied using a screwdriver or screwdriver attachment fitted to an electric drill. Due to the threaded nature of this fastener, it can offer a level of grip that is unmatched by the nail. Generally made from carbon steel wire, the screw is used in a multitude of situations for temporary to long term joining. Screws are great choice, for example, for attaching a lid to a crate that will need to be removed after being installed.
Fastener Type 3: Staples
As a fastener, staples were originally introduced as a solution to paper fastening. Early staples were crudely driven into stacks of paper, but crimping the ends of the staple had to be done by hand.
Bostitch, an American company, introduced the first “portable stapling machine” in 1914. That simple invention paved the way for the modern staple guns used in the industrial packaging industry today. In the modern wood packaging industry, staples are almost always installed using a pneumatic staple gun or a similar type of air driven tool.
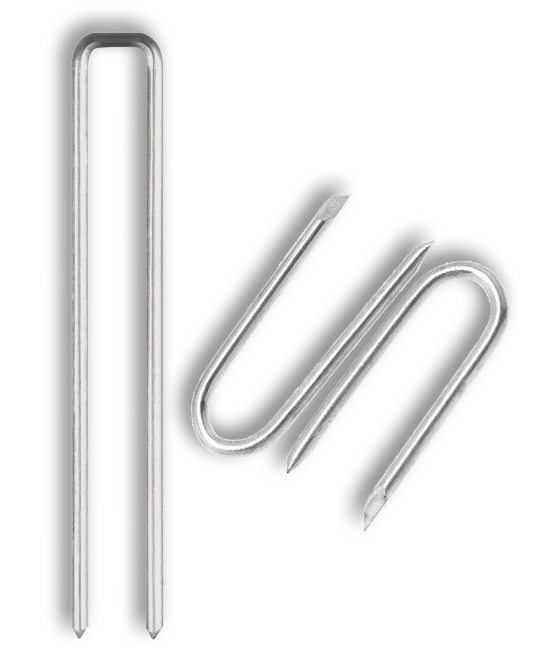
These fasteners are great in situations where the thickness of the material is too thin for a nail or screw such as plywood or OSB panel. In the wood packaging industry, a staple is most commonly used in joining “cleating” or strips of lumber to panels on crates near the edges to give additional support and strength to a crate itself. Staples can also be used in a variety of situations that not only include wood to wood joints, but also in attaching packing materials such as foam or bubble wrap.
Determining Fastener Size
Regardless of the type of fastener you use, the size of the fasteners for your application is dependent on several variables. Generally, it’s optimal to achieve 1.5 inches of penetration into the wood. This allows the best chance for the nail, staple, or screw to achieve the necessary connective strength without damaging the wood it is connecting.
Oftentimes, 1.5 inches of penetration is not possible due to the thickness of boards that the fasteners are connecting. In that type of situation, it is best to choose a fastener that will offer the most penetration without protruding through the other side of the material.
For example, if you were connecting a 1×4 to another 1×4, you would only have a total of 1.375 inches of wood when the two pieces are placed together. It wouldn’t be possible for the fastener to drive 1.5 inches into the final piece of wood, since the final piece of wood in this instance is approximately 0.6875 inches thick. In this type of scenario, we would choose a 1.25 inch staple instead.
It is also important to consider countersinking.
Don't forget about countersinking when determining the penetration of a wood fastener. If you forget, your nail will protrude through the other side and cause problems. Click To TweetRarely will a fastener that is pneumatically driven be exactly flush with the wood it has been driven into. More often than not, the fastener will be slightly below the surface of the wood. If countersinking isn’t considered, over-penetration can quickly become a problem, and cause fasteners to protrude through the other end of the final piece of wood.
Which Fastener Should Be Used?
Knowing the right type of fastener to use in any type of pallet or crated design can sometimes be a relative gray area, with no definite right or wrong answer. Industry standards guide designers and builders in the right direction in most cases, but many circumstances require a keen knowledge of the industry. It also helps tremendously to have a clear idea of the customer product being handled, stored, and transported.
For instance, a cleated panel sub-assembly, such as a crate face or crate lid, will be held together by staples in almost every instance. Deck boards and the assembly of a crate’s base, sides, ends, and top will almost always be fastened using nails. In more abnormal scenarios, lag screws, all thread, eye bolts, or mending plates may be used in place of nails and staples.
Wood selection is also commonly made with a fastener type in mind. Different types of wood have different wood density, and that can affect fastener choice.
Lastly, the time it will take to assemble a wood packaging product should always be in the design thought process when choosing fasteners. For example, the designer and/or builder may choose to use doubled-up 2x4s instead of a 4×4 to avoid having to apply lag screws and/or all thread to the assembly, since nails are much easier and faster to apply than predrilling and securing with large screws.
Industry standards are helpful when choosing which type of fastener to use in a common wood package, but the type of fastener that will work best in an application is not always crystal clear. There are often multiple options that will work. Many types of wood packaging solutions must be handled on a case-by-case basis. That’s why working with a packaging expert is often necessary.
How Many Fasteners Should Be Used?
Determining the quantity of fasteners to use in an application is just as important as choosing the proper fastener and the right size. The number of fasteners used in a wood package assembly can prove to be critical in the design and building processes. Industry standards help to guide a wood packaging designer to apply an adequate number of fasteners based on certain circumstances, but common sense and knowledge of the product can compliment industry standards in less-than-standard applications.
In a simple case, the number of fasteners needed to apply a deck board to a stringer is simple and uniform. A 1×4 deck board will almost always be fastened to its stringer using two 2.25 inch nails at each connection. A simple and uniform fastening schedule is found to be true for the majority of common lumber connections found in pallets and crates.
A more abnormal connection, such as a 4×6 to another 4×6, will call for the use of a much larger fastener and we may not have an industry standard to make things objectively black and white. In this example, the designer or builder may choose a 3/8-inch x 6 inch lag screw, or even a single piece of all-thread with nuts and washers.
Both of these solutions can be acceptable, and the decision may simply come down to what’s currently in inventory, and what’s the most cost-efficient solution.
Why Do Fasteners Fail?
In general, fasteners fail for one of two reasons:
- Withdrawal – the fastener working its way out of the wood. This is considered a parallel failure.
- Bending/Shear – the fastener bending or breaking under stress. This is considered a perpendicular failure.
Many of the same factors that will affect the withdrawal strength of a nail, will also affect the bending or shear. With nails, resistance to withdrawal is directly related to the density of the wood, the diameter of the nail, and the depth of penetration. The surface condition and the type of shank also factor into the resistance to withdrawal1.
In the wood pallet and crate industry, the lion’s share of all pallets are manufactured from Southern Yellow Pine (SYP), which ranks very high among softwood species in density. Hardwoods can certainly offer higher densities, but can be pricey, especially when compared to the economy grades of SYP.
The diameter of the nail directly and significantly affects its holding power. Simply put, the larger the diameter of the nail, the more surface area exists for a nail to make contact with the surrounding wood fiber.
While the diameter of the nail will affect the amount of surface area in contact with the wood, the surface finish of the nail will affect the method of the nail-to-fiber contact. Using screw shank or ring shank nails will provide a grooved surface to enhance the strength of the nail against withdrawal.
The depth of penetration into the receiving piece will also directly influence the strength of a nail, increasing again the amount of surface area of the nail making direct contact with the wood fiber. It is important to choose a nail that is of sufficient diameter and length, and is manufactured with optimal shank design to reduce withdrawal and shear.
Screws, on the other hand, will always offer a greater resistance to withdrawal, but will typically offer less resistance to bending or shearing forces than nails. If you are concerned mainly with the fastener pulling out, use a properly sized screw exclusively, or incorporate screws into various locations in the design.
Screws are also a good option when the longevity of service is an important factor.
As wood components age and are exposed to weather conditions, shrinkage in the wood can occur around the fasteners reducing the surface area of contact between nails and wood fibers. In these instances, the threaded construction of a screw will offer much more holding power than that of a nail, especially a bright, smooth shank nail.
As we’ve already discussed, screws also allow for the removal of components, such as lids or sidewalls, that must be removed for loading and unloading of product. However, it’s important to remember that screws are much more costly than nails and will affect your overall price for a pallet or crate. The price difference for screws can be dramatic, especially when you consider the not only the cost of the fastener, but also the extra labor to place each one.
Looking for manufacturing tolerances for wood fasteners? Your manufacturer should be able to provide you with spec sheets - just ask! Click To TweetAs a rule in the wood packaging industry, ASTM F1667 provides manufacturing tolerances for fasteners. Manufacturers should be able to supply corresponding test data, in the form of product specification sheets, for all fasteners. Product Specification Sheets provide information related to the material of construction, surface finish, Fastener Withdrawal Index (FWI), Fastener Shear Index (FSI), and the MIBANT results for a particular fastener. These characteristics and test results will help confirm the strength through ASTM certification, and will supply comparative data on the strengths of various choices of fasteners.
Wrapping It All Up
As you can see, there is a lot of testing, industry know-how, and experience required to choose the correct fastener for each application. The longevity, durability, and strength of your wood packaging largely depends on making the right fastener choice for each application. A well-designed wood pallet or crate requires designers to have a keen understanding of which fastener works best for the application, the optimum number of fasteners required, and the correct size of fasteners for your wood packaging design.
As a customer, fasteners might not be the first thing you think of with regards to your wood packaging, but it’s a crucial component of any application. The right wood fasteners help to get your product to its destination safely. Here at Conner, you can be sure that we’ve got it covered.
Author: The Conner Packaging Design Team
The Conner Packaging Design Team makes the magic happen. Made up of packaging engineers, costing advisors, and subject matter experts, this team of professionals ensures that the wood packaging we produce is the best solution possible for your unique application.The Conner Packaging Design Team makes the magic happen and ensures the best solution for your unique application. Click To Tweet
1. US Department of Agriculture (1965). Nail-Withdrawal Resistance of American Woods. Report FPL-093. Forest Products Library, Madison, WI